Unsere Anlage
1. Bestückung
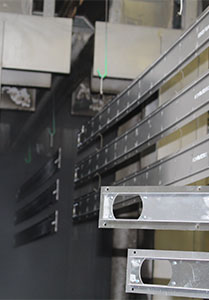
Hier werden alle zu beschichtenden Teile mittels Lackierhaken an einer Deckenförderanlage fixiert. Die Deckenförderanlage verbindet alle nun folgenden Stationen miteinander, sodaß die Teile erst nach Fertigstellung zur Verpackung dem Förder wieder entnommen werden.In der Regel liegt die Bandgeschwindigkeit bei ca. 2 Metern pro Minute.
Hierbei ist es wichtig, dass alle zu beschichtenden Bauteile genügend Bohrungen haben, um eine sichere Fixierung zu gewährleisten.
Außerdem gilt:
Die Beschichtung wird umso günstiger, je mehr Teile untereinander gehängt werden können!
2. Vorbehandlung
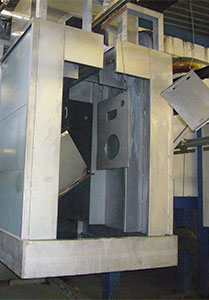
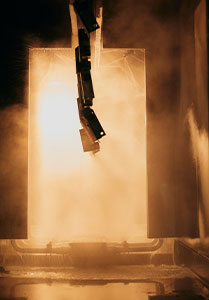
Vorbehandlung
Da eine Beschichtung nur so gut sein kann, wie die Entfettung und Vorbehandlung der Bauteile, haben wir uns dazu entschlossen, eine Anlage zu installieren, die technisch auf dem allerneusten Stand ist:
Wir arbeiten mit einer 5 –Zonen Spritzanlage, welche vollständig aus Edelstahl gefertigt wurde, und folgende Behandlungsschritte liefert:
- Entfetten
- Phosphatieren
- Stadtwasserspüle
- VE Wasser Spüle
- Passivierung als „no rinse“ Stufe
Durch die Passivierung sind wir in der Lage auch auf Aluminium und verzinkten Bauteilen besten Korrosionsschutz und beste Haftungsergebnisse zu erreichen.
Bitte beachten sie, das unsere Passivierung kein umweltschädliches Chrom verwendet und somit den neusten Umweltanforderungen gerecht wird.
Zusätzlich ist nach jeder Behandlungsstufe ein Zwischenspülring integriert.
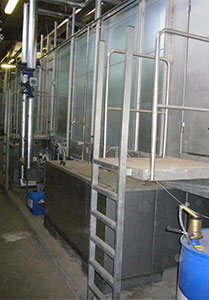
Unsere Anlage arbeitet abwasserfrei:
Durch permanenten Austausch der Spülen erreichen wir beste Ergebnisse. Das Abwasser der Spülen verwenden wir dann aber noch, um damit die Wasserverluste in den beheizten Entfettungs- und Phosphatierungszonen auszugleichen.
Um den modernen Umweltanforderungen gerecht zu werden, wird entstehendes Abwasser der beiden Aktivzonen durch die Abwärme des Einbrennofens verdampft. Der Entstehende Schlamm wir dann einer fachgerechten Entsorgung zugeführt.
Für gleichbleibende Vorbehandlungsqualität werden bei uns alle Chemikalien kontinuierlich und voll automatisiert zugegeben.
Zum Thema Oberflächenqualität sorgen in die Aktivzonen eingebaute Hochleistungsfilteranlagen für ein permanentes Ausfiltern des entstehenden Reaktionsprodukte. Unsere Oberflächen sind daher weitestgehend frei von Einschlüssen und Filmstörungen durch Vorbehandlungsrückstande. Die VE Spüle und die integrierte Rückspülkaskade trägt Ihren Teil dazu bei, den wachsenden Anforderungen unserer Kundschaft an die gelieferten Oberflächen gerecht zu werden.
3. Haftwassertrockner, Kühlstrecke 1
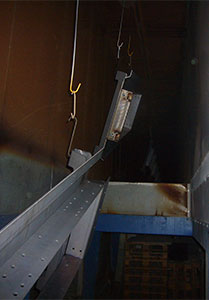
Haftwassertrockner
Der Haftwassertrockner ist eine Nebenkammer des Einbrennofens. Hier werden alle Bauteile, welche von der chemischen Vorbehandlung noch nass sind, durchgefahren, um diese zu Trocknen. Das geschieht bei einer Temperatur von ca. 160°C.
Außerdem werden in diesem Trockner alle feuerverzinkten Bauteile getempert, was bedeutet, das aus dem Zink austretende Ausgasungen, mit den daraus resultierenden Filmstörungen im Pulverlack, jetzt schon ausgetrieben werden.
Im Weiteren wird im Haftwassertrockner die in der chemischen Vorbehandlung aufgebrachte Passivierungsschicht eingebrannt.
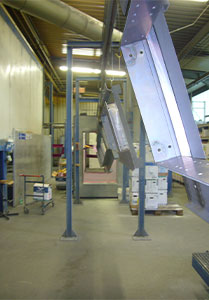
Kühlstrecke 1
Nach dem Haftwassertrockner ist eine Kühlstrecke nachgeschaltet, um die erhitzten und getrockneten Teile auf eine Temperatur von ca. 40 ° C abzukühlen. Dieser Schritt ist notwendig, um eine vorzeitiges “Anbacken” des aufzubringenden Pulverlackes während der Beschichtung zu verhindern. Auf dieser Kühlstrecke laufen die Teile auf unsere beiden Pulverzentren zu. (Im Hintergrund zu erkennen)
4. Die Beschichtung
Unsere Anlage ist mit zwei Beschichtungskabinen ausgestattet:
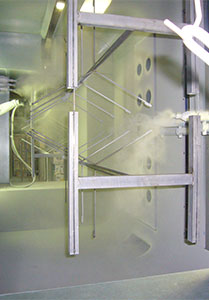
Die Rückgewinnungskabine
Hier werden große Serien mit hohen Losgrößen in gleicher Farbe beschichtet. Die Beschichtung kann von Hand, aber auch automatisch mit Hubgerüsten vorgenommen werden. Vorteil der Automatikbeschichtung ist eine gleichbleibende Schichtstärke und Qualität der Teile. Sie kann aber nur bei einfachen, möglichst zweidimensionalen Geometrien angewandt werden. Der nicht am Teil haften bleibende Pulverlack wird zu 100 % zurückgewonnen und wiederverwendet. Nachteilig ist die lange Rüstzeit der Kabine während des Farbwechsels von einer Farbe auf eine andere, daher ist dieses Verfahren nur bei mittleren bis großen Losen einsetzbar.
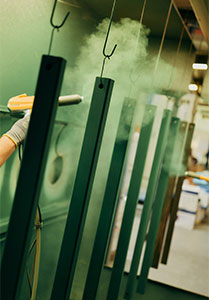
Die Verlustkabine
In der Verlustkabine werden nur Aufträge in kleinen Losgrößen beschichtet. Hier wird nur von Hand beschichtet, und nur im Verlust, d.h. der nicht am Bauteil anhaftende Pulverlack wird abgesaugt und nicht wiederverwendet. Vorteil: Eine aufwendige Reinigung der Kabine beim Farbwechsel entfallt, dadurch Rüstzeiten von wenigen Minuten beim Farbwechsel. Nachteilig ist der erhöhte Pulverlackverbrauch.
5. Durchlauftrockner, Kühlstrecke 2
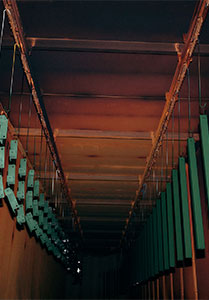
Durchlauftrockner
Der Pulverlack haftet nun nur aufgrund der aufgebauten elektrostatischen Aufladung an den Bauteilen, wäre also noch jederzeit mit Druckluft vom Bauteil zu entfernen.
Die Aushärtung erfolgt nun in der Trockenkammer bei einer Temperatur von ca. 200 °C. Um eine optimale Aushärtung und somit Haftung des Pulverlackes zu erreichen, sind die Einbrennbedingungen von Bedeutung. Diese können bei Pulverlacken erheblich differieren. In der Regel aber ist für die Härtung eine Objekttemperatur von min. 180°C über eine Haltezeit von 10 Minuten vorgeschrieben. Diese Prozessparameter sind insbesondere bei dickwandigen Stahlteilen über t=3 mm zu beachten!
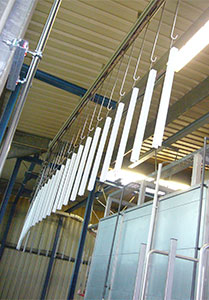
Kühlstrecke 2
Der Trockenkammer ist die 2. Kühlstrecke nachgeschaltet. Hier werden alle Bauteile von 180°C wieder auf Raumtemperatur heruntergekühlt, um anschließend verpackt zu werden.
Man bedenke:
Die Bauteile sind sofort nach dem Abkühlen montagefähig. Ein weiteres Trocknen wie im Nasslackbereich üblich, entfällt vollständig.
6. Qualitätskontrolle, Verpackung
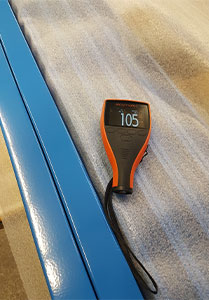
Qualitätskontrolle durch Schichtdickenmessung
Nach der Beschichtung werden alle Bauteile wieder Transportsicher verpackt. Dabei werden alle Teile einer Sichtkontrolle unterzogen und stichprobenartig Schichtdickenmessungen vorgenommen. So lässt sich überprüfen, ob die Bauteile den geforderten Korrosionsschutzanforderungen von C1 bis C5 gerecht werden.
Alle Messprotokolle werden digital gespeichert und können dem Kunden gerne als PDF übermittelt werden.
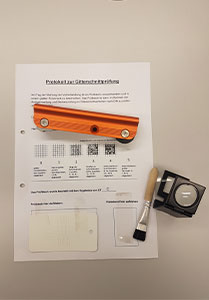
Qualitätskontrolle durch Gitterschnitt
Wöchentlich, aber auch auf Wusch des Kunden, werden Prüfbleche in der Serie beschichtet, bei welchen dann eine Gitterschnittprüfung nach DIN vorgenommen wird, um die Haftfestigkeit des Pulverlackes zu beurteilen. So können Rückschlüsse auf die Vorbehandlung und Einbrennbedingungen gezogen werden. Durch unsere Qualitätskontrollen können wir sicher stellen, dass nur einwandfreie Ware unser Haus verlässt.
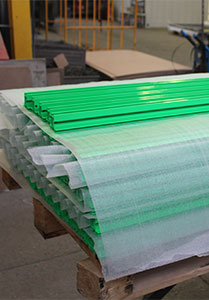
Verpackung
Wir verwenden für die Verpackung unserer Produkte Kartonagen, Styropor, Schaumfolie und Kanthölzer, um einen sicheren Transport zu unseren Kunden zu gewährleisten und Beschädigungen auszuschließen.
Abschließend werden die Teile mit Umreifungsband oder Stretchfolie auf den Paletten gesichert und in unserem Regallager eingelagert, bis der Auftrag vom Kunden abgerufen und verladen wird.